The Process | Tarapath | low pressure moulding
low pressure moulding is a process that sits between conventional injection moulding and traditional potting or casting processes.
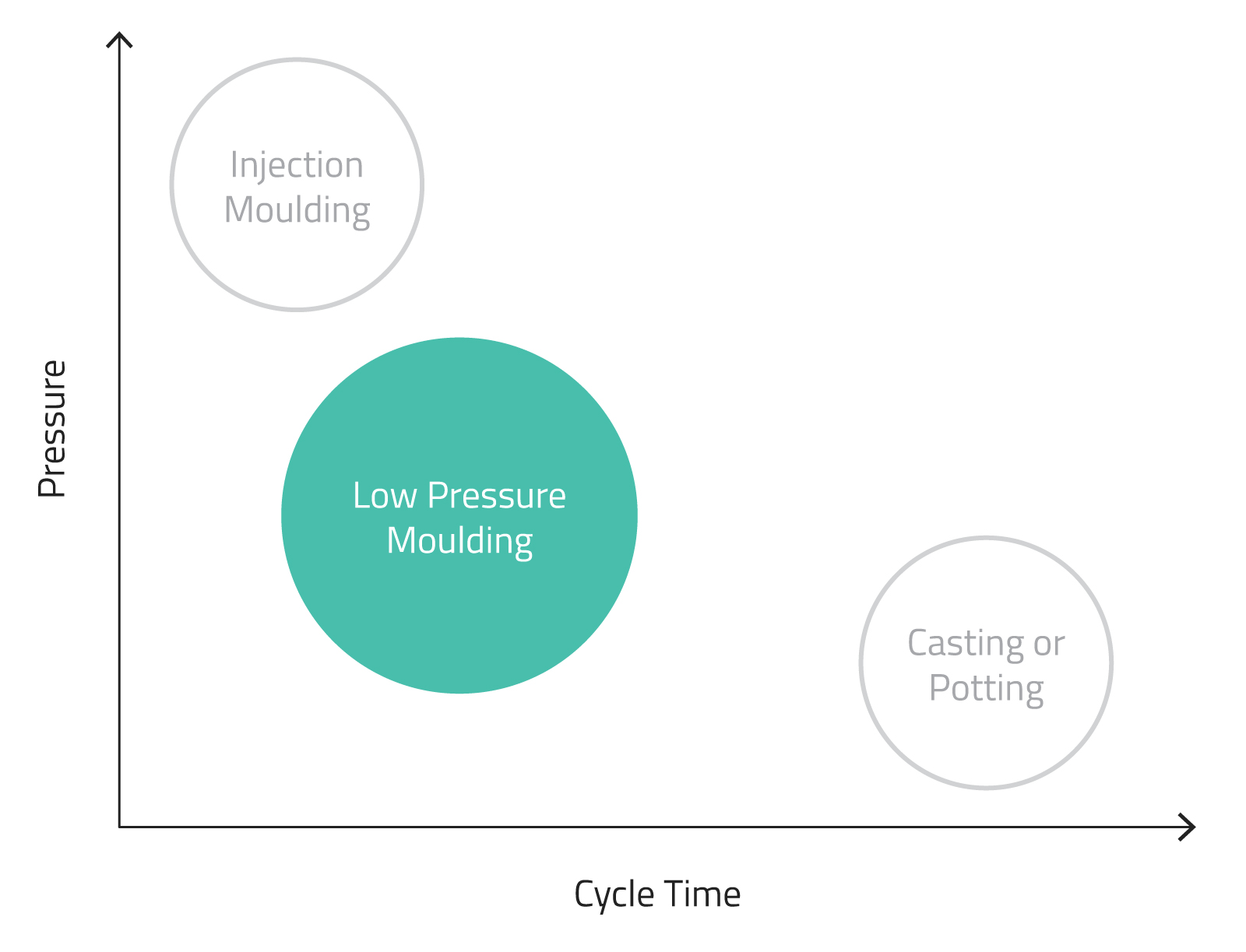
The use of a simple die set allows for the production of a wide variety of encapsulated electronics.
Be it PCB encapsulation, cable harness strain relief, wire connectors and splices, sensors, security electronics to agricultural products, low pressure moulding is the go-to solution for reliable and economical protection and encapsulation.
To understand how low pressure moulding can improve your product, and even your business, it is helpful think of the '4R approach'.
REPLACE. REDUCE. RE-USE. RETHINK.
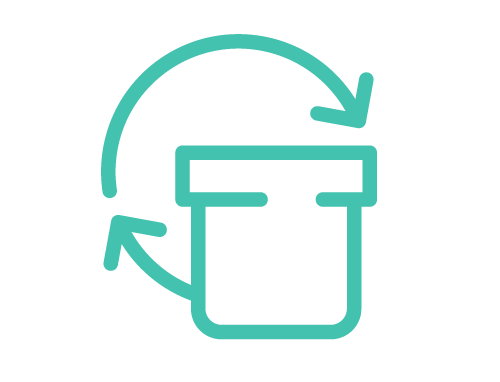
Replace
Replace traditional potting, sealing and conformal coating which can be costly.
Replace old thinking with innovative processing
low pressure moulding provides the opportunity to replace traditional potting, sealing and conformal coating processes, which can be wasteful and costly, and/or standardised off-the-shelf products with a more innovative form of electronics encapsulation designed specifically for your product.
Curing time
Potting
24–72 hours
Sealing
48–72 hours
Conformal Coating
4–12 hours
Low Pressure Moulding
No curing required
BOM part numbers required
Potting
5–7 part numbers
Sealing
5–7 part numbers
Conformal Coating
3–4 part numbers
Low Pressure Moulding
1 part number
Process steps
Potting
Up to 8 steps
Sealing
Up to 6 steps
Conformal Coating
Up to 8 steps
Low Pressure Moulding
3 steps
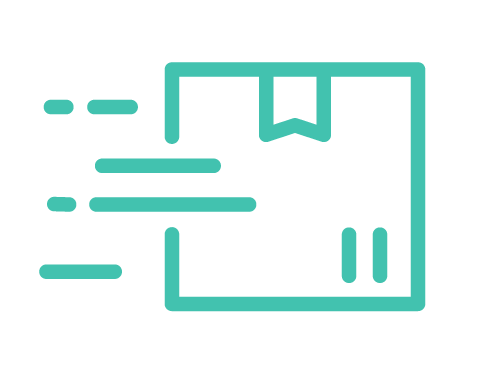
Reduce
Reduce material, cycle time, equipment and operations footprint.
Reduce material
The low pressure moulding process creates the opportunity to make serious reductions that are good for your product, and even better for your bottom line.
The ability to “skyline” components and electronics, rather than fill up an enclosure, means that the amount of material used for each product can be dramatically reduced.
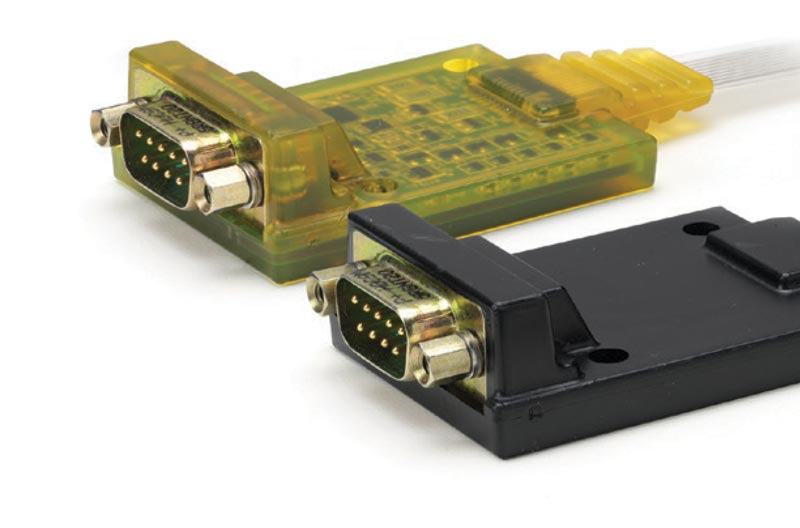
The traditional potting process
STEP 1
Enclosure
Moulded housing or off-the-shelf housing modified
STEP 2
Palletise
STEP 3
Insert & Assemble
Electronics, screws, grommets, spacers, etc.
STEP 4
Preheat Parts
STEP 5
Dispense
STEP 6
Vacuum or Settle
STEP 7
Cure
Requires valuable floor space for up to 48 hours
STEP 8
Test
Reduce cycle time
When you replace traditional electronics potting with the low pressure moulding Process you are replacing up to 8 steps with 3 simple steps.
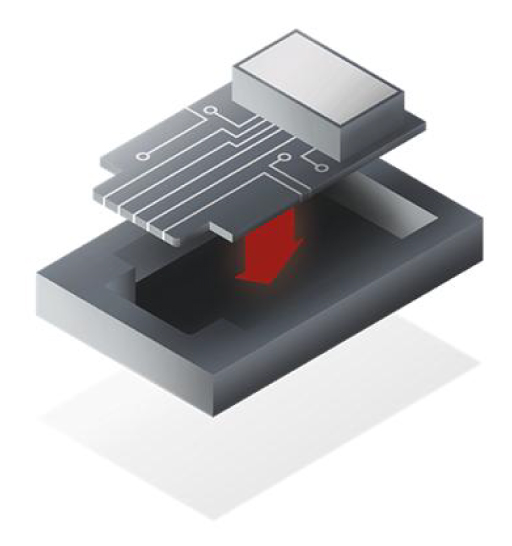
STEP 1
Insert electronics
Insert parts directly into the mould set.
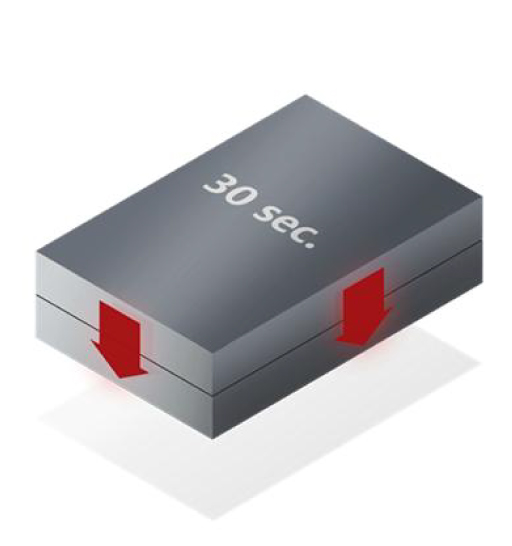
STEP 2
Mould
30 sec – 2 min encapsulation process.
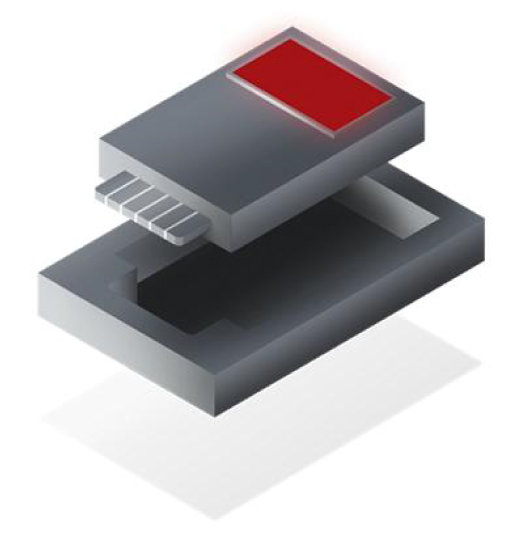
STEP 3
Test device
Parts handled immediately after moulding.
Reduce Equipment and Operations Footprint
low pressure moulding requires significantly less space than potting and conformal coating processes. Space savings come from not requiring – storage for WIPS that are curing – Conformal Coating spray booths – Dispensing Equipment – Vacuum Chambers – Extraction systems.
They can be replaced with a single low pressure moulding Machine.
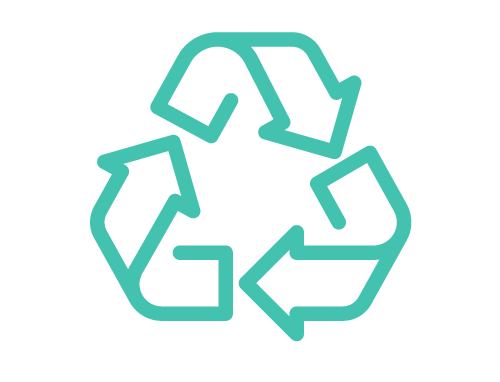
Reuse
Re-use, recycle and reconsider the effect of your product on the environment.
Think Sustainability with low pressure moulding
Re-use, Recycle and Reconsider the effect of your product on the environment.
low pressure moulding equals zero waste. All excess material in the form of sprues is completely recyclable.
Materials are made with natural ingredients, there are no harmful fumes from the moulding process, and materials are RoHS and REACH compliant.
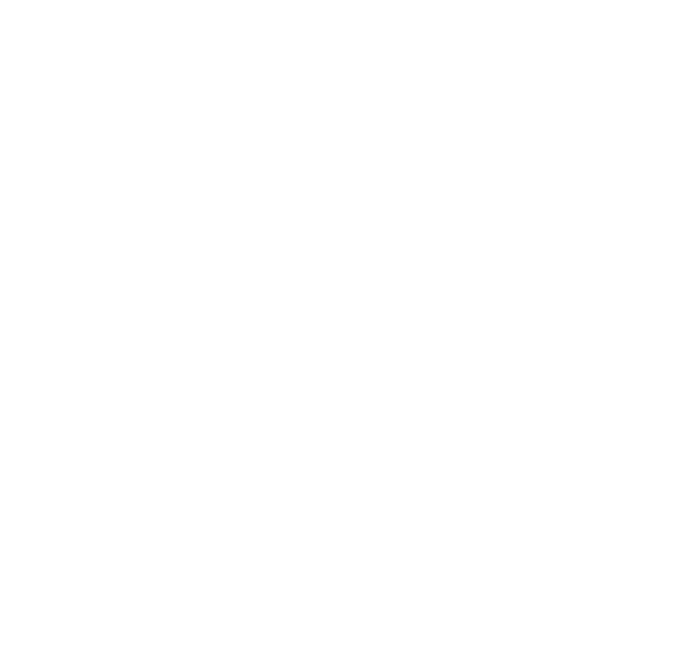
Rethink
low pressure moulding allows you to rethink what your product can be.
Design Freedom
The low pressure moulding process allows designers and engineers greater flexibility when designing products when compared to housing electronics in enclosures.
If you are looking to keep the form factor to a bare minimum for fitment into larger assemblies, low pressure moulding allows the minimum amount of material to be used through skylining and without the need for an enclosure.
low pressure moulding allows the encapsulation to be the enclosure. This means design elements such as logos, graphics, surface treatments can be moulded directly onto the surface of the part. Achieving this level of sophistication without a high level of additional assembly is not possible with other manufacturing processes.
Product Optimisation
With low pressure moulding, there is no need to compromise. The range of Technomelt materials (link to materials page) provides options which allow you to utilise a lightweight material with excellent adhesion to various subsrates, high resistance to environmental factors, all with a safe, 1 component material.
Cost
low pressure moulding can be a major driver in cost reduction for your products, as well as your operations. Whether it is the reduction in items in bills of materials, the increased throughput that can be achieved, the relatively low capital equipment costs or the reduced WIPs on the factory floor, the savings can be significant.
Let us assess your product and see if low pressure moulding is the solution you’ve been looking for!
Question?
Let us assess your product and see if Low Pressure Moulding is the solution you’ve been looking for.